5-Axis Equipment
Five-Axis Machining: Precision & Efficiency at ZK Precision Technology
At ZK Precision Technology, our five-axis machine delivers unmatched capabilities for machining complex geometries with exceptional precision and tight tolerances. By reducing setups and handling multiple sides in a single operation, we ensure efficiency and accuracy while achieving superior surface finishes. This advanced technology shortens lead times for faster production and extends tool life through optimized cutting angles—reducing costs and enhancing performance. Trust ZK Precision Technology for intricate, high-quality components that meet the most demanding standards.
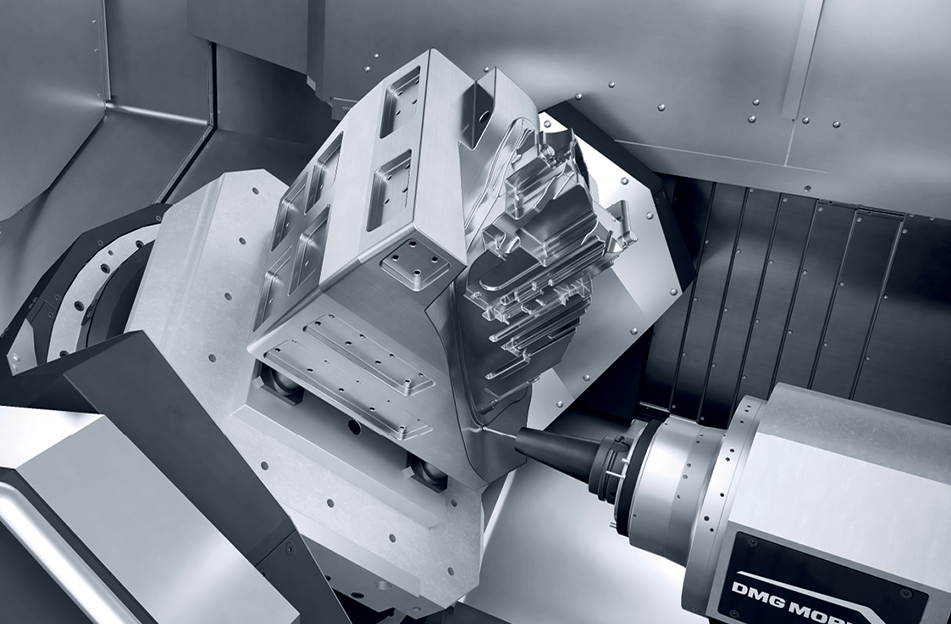
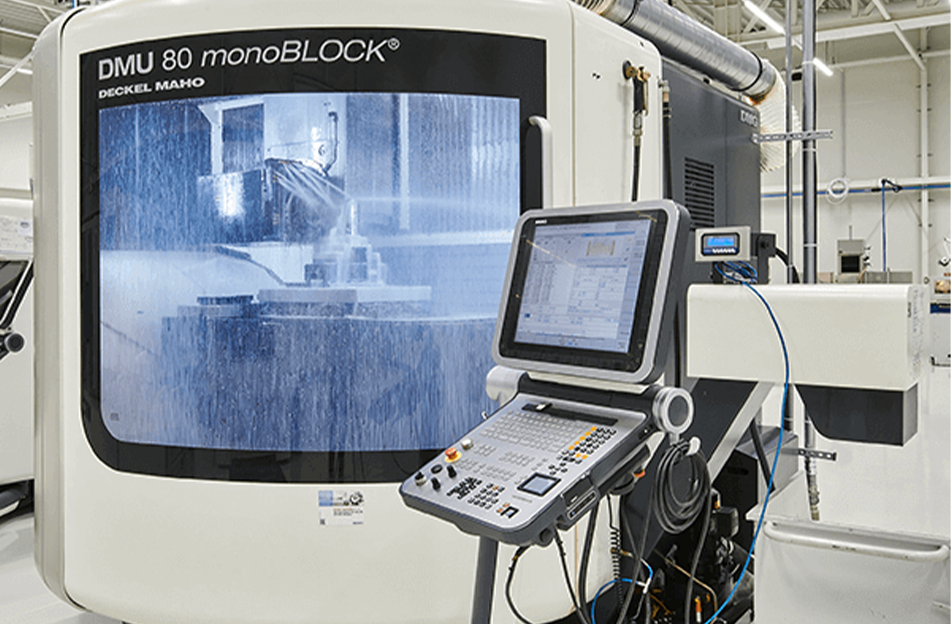
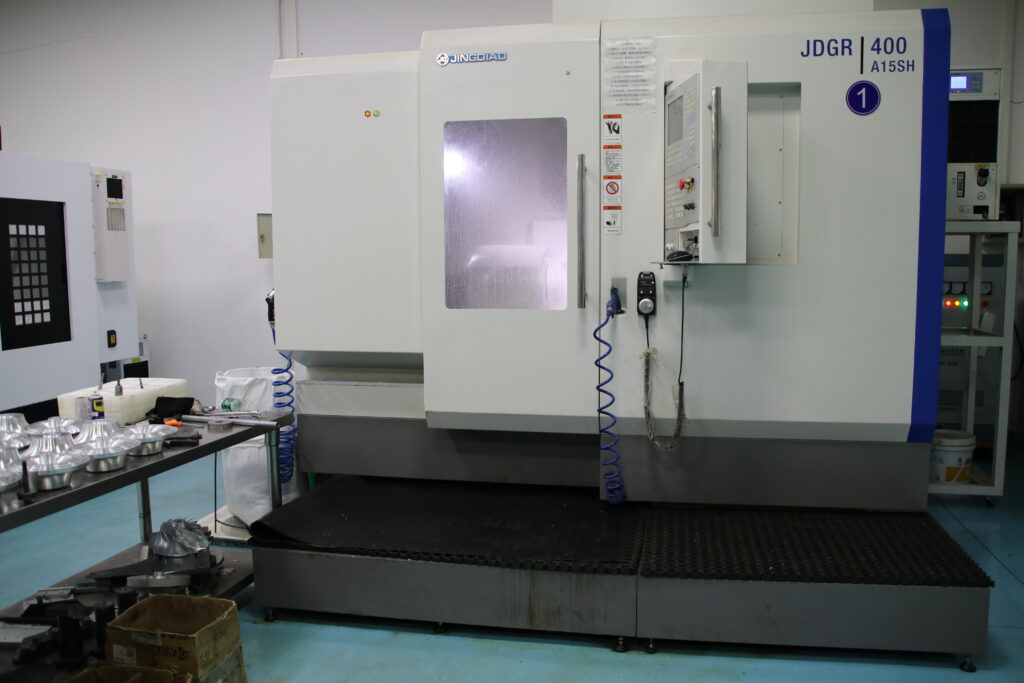
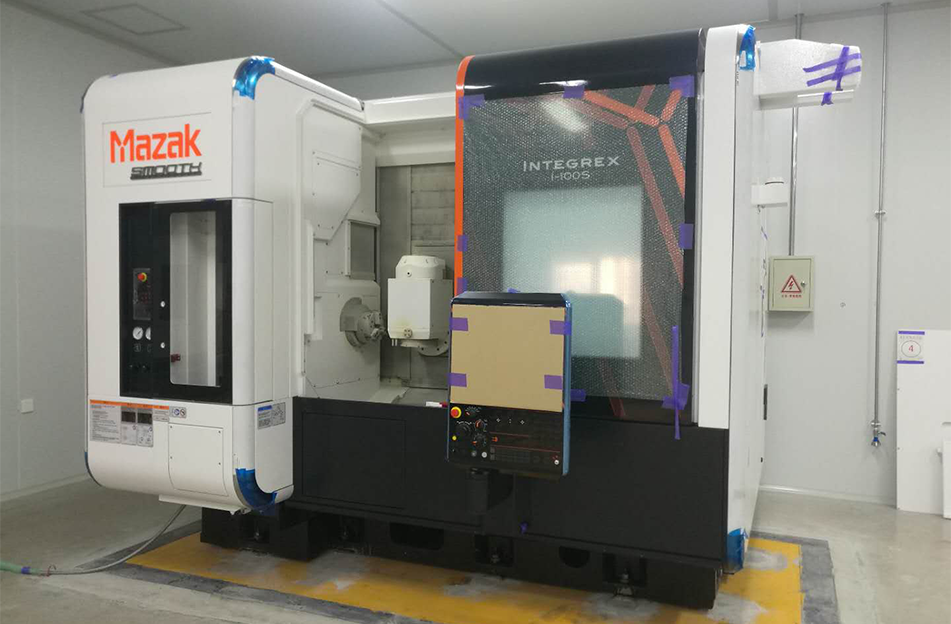
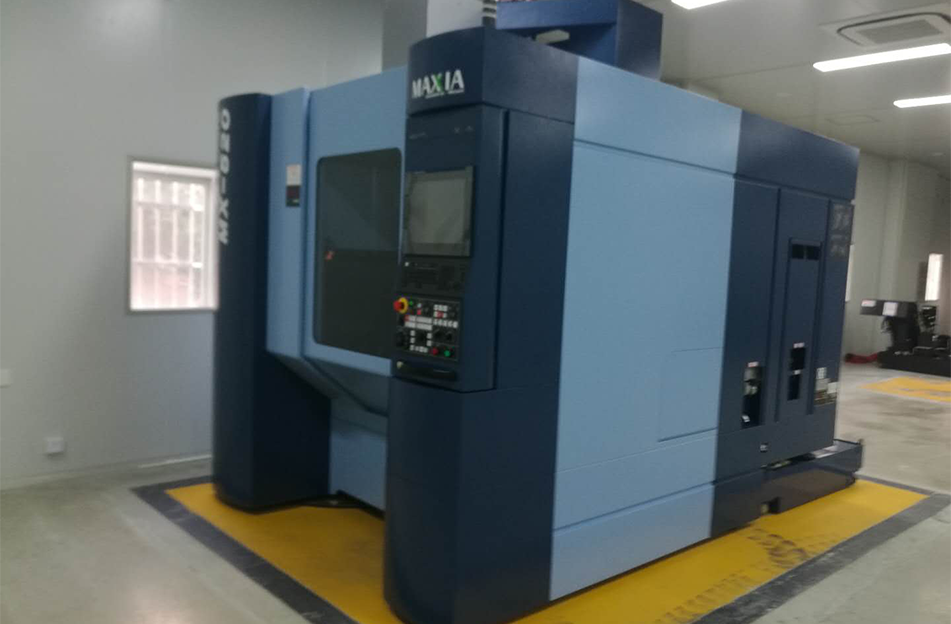
FAQs
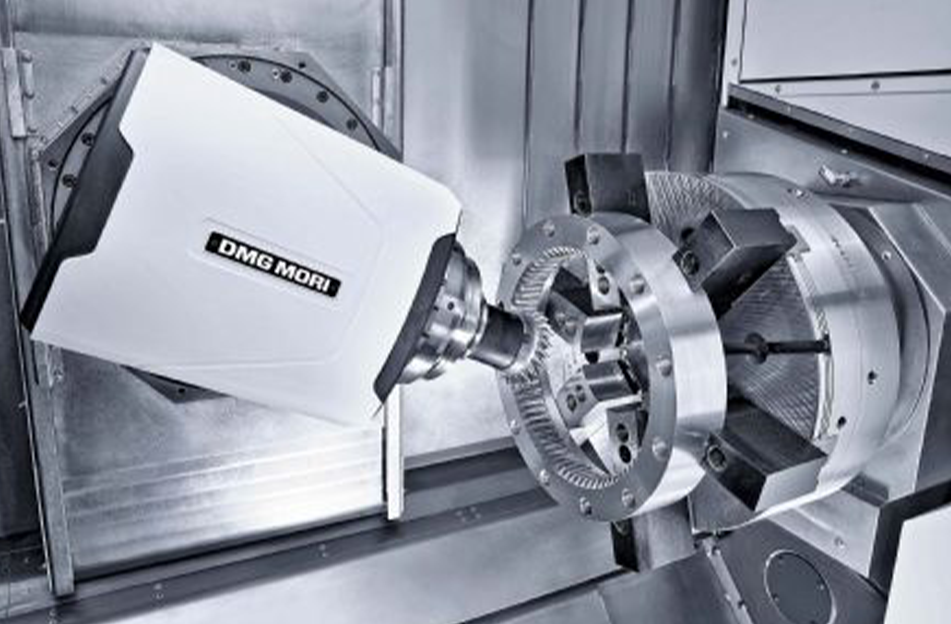
Customers benefit from complex, high-precision parts produced in shorter lead times with better surface finishes. It’s ideal for intricate designs and reduces the need for multiple setups, saving time and cost.
While it may have higher upfront costs, it often reduces overall expenses by minimizing setups, improving efficiency, and producing higher-quality parts with fewer errors.
Industries like aerospace, automotive, medical, and energy benefit from its ability to produce complex, high-tolerance components.
Five-axis machining reduces production time by handling multiple operations in one setup, making it faster than traditional methods for complex parts.
Five-axis machines can handle a wide range of materials, including metals, plastics, and composites, making them versatile for various industries.
Five-axis machining products
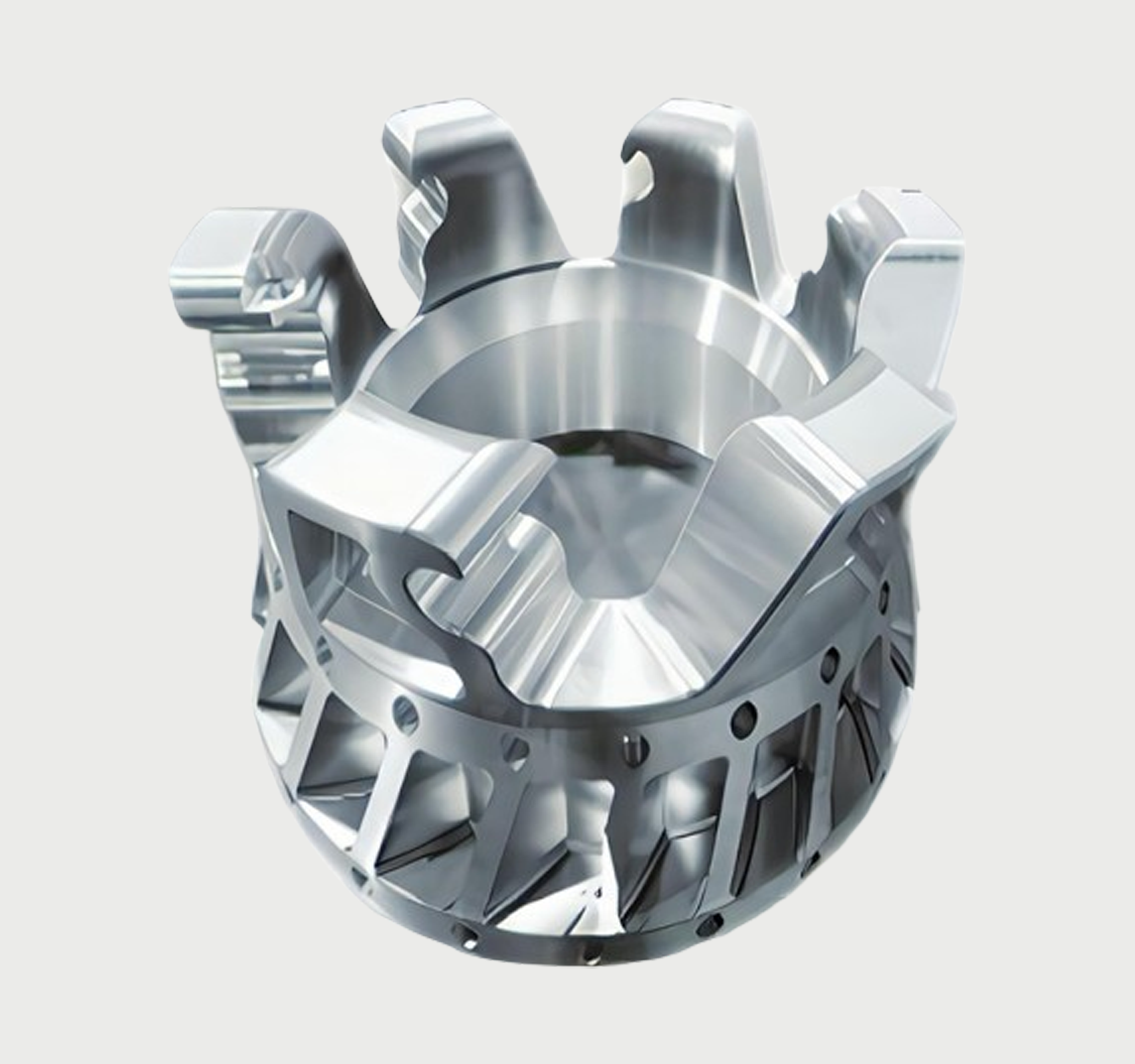
Base
The base is a precision-engineered component with dimensions of 30x50cm, crafted from high-quality materials including CuZn39Pb1, C3600, CZ122, CuSn6, CA104, C10100, C12000, H62, and QSn7-0.2. Manufactured to a precision tolerance of 0.01mm, it is produced using advanced processing methods such as CNC turning and knurling. To enhance corrosion resistance and surface aesthetics, the base undergoes specialized treatments including nickel plating, zinc plating, chromium plating, blackening, and phosphate treatment.
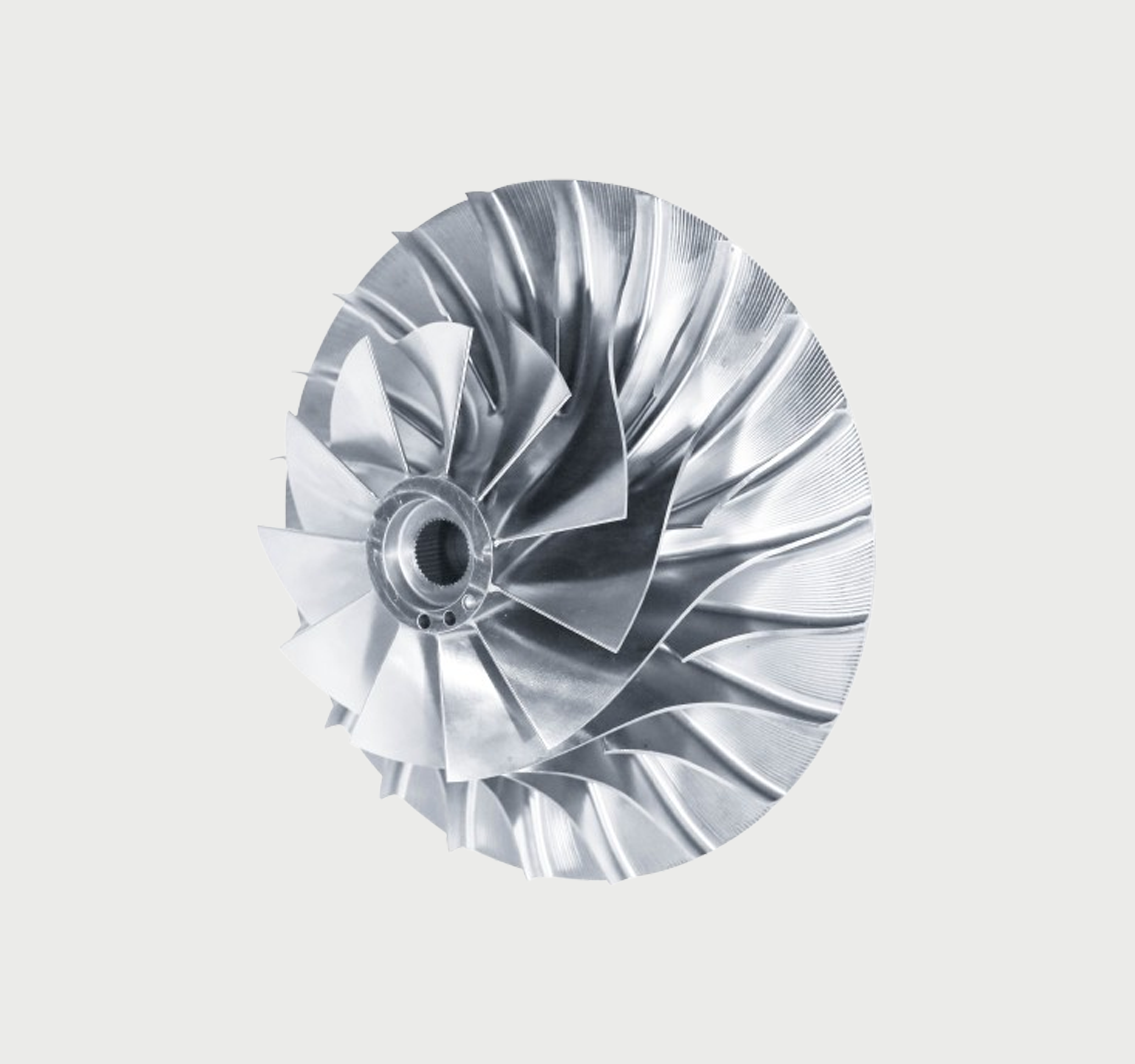
Turbine blades
Turbine blades are high-precision components with a size of 60x60cm, fabricated from robust materials such as 65Mn, 1.1221, C60, Gr15, SUJ2, and 100Cr6. Engineered to a remarkable precision of 0.005mm, these blades are crafted using advanced processing techniques including CNC turning, CNC milling, wire cutting, and grinding. To enhance strength and durability, they undergo heat treatments like carbonitriding and hardening to achieve a hardness level of HRC40-45.
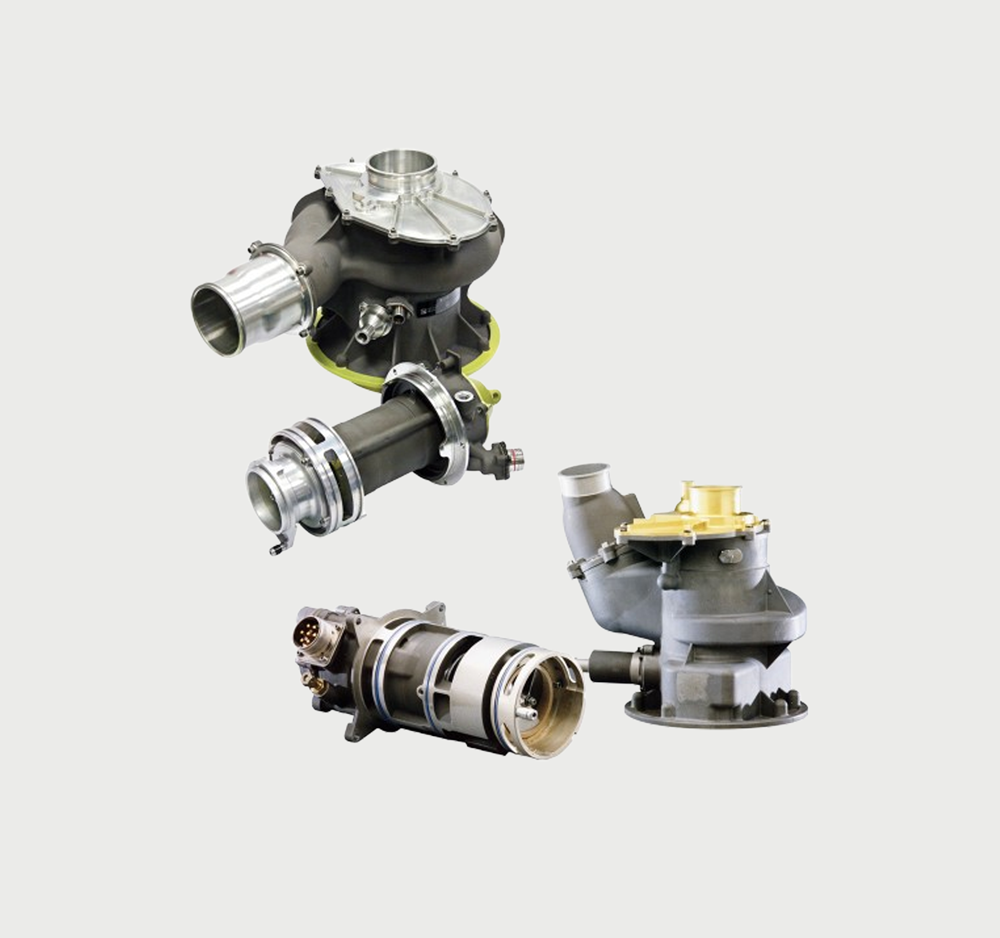
Fuel System
The fuel system is a precision-engineered component with dimensions of 85x85x140cm, constructed from high-performance materials such as PEEK, PTFE, POM, PA66, ABS, PBT, PC, and PE. Designed to a precision tolerance of 0.01mm, it is manufactured using advanced processing techniques, including CNC milling, CNC turning, internal and external cylindrical grinding, boring, and deep hole processing. These methods ensure exceptional accuracy and durability, meeting the stringent requirements of fuel system applications.
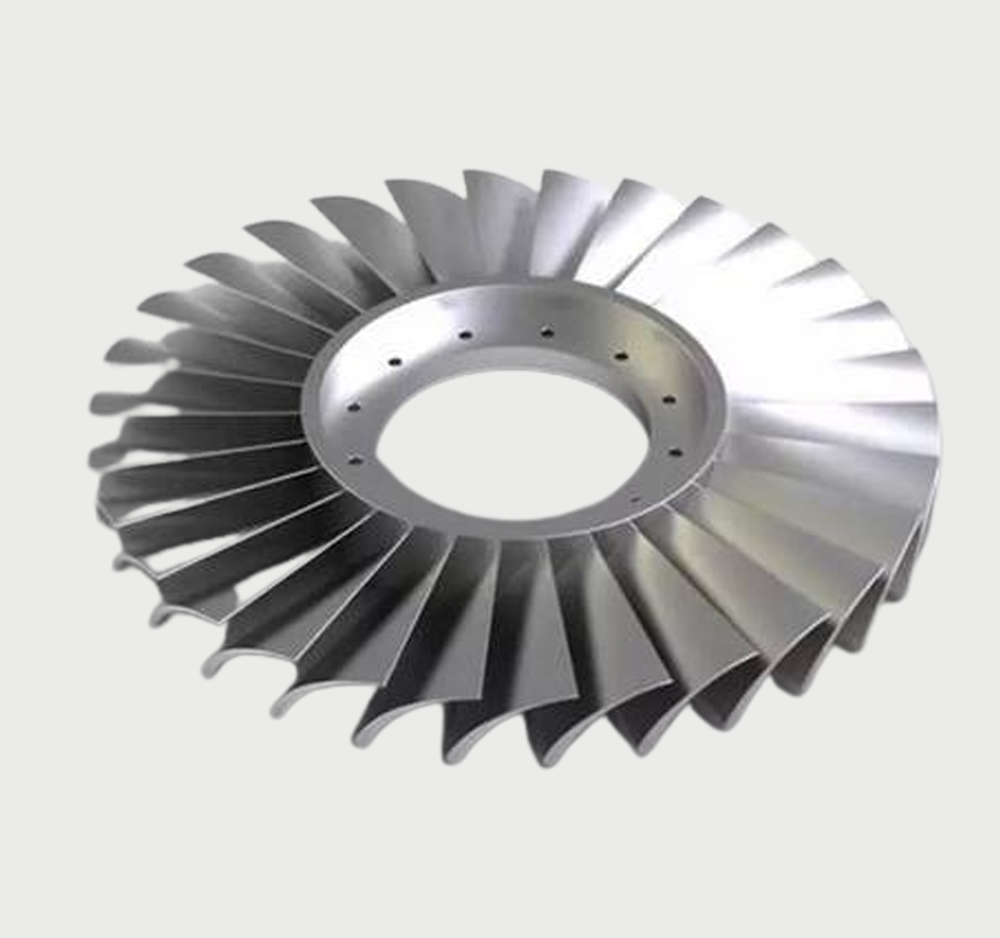
Blades
Blades are customizable precision components tailored to specific requirements, manufactured from premium aluminum alloys such as 7075-T6, AlZn5.5MgCu, 6082-T6, 5083-T5, and 6063-T6. With a precision tolerance of 0.01mm, these blades are expertly crafted using advanced techniques like CNC milling, 5-axis machining, and surface grinding. To ensure superior surface quality and enhanced durability, they undergo specialized treatments including sandblasting, hard anodizing, brushing, and spraying.

Fuel accessories
Fuel accessories are precision-engineered components with dimensions of 100x280x400mm, made from robust materials including SKD11, SKD61, D2, SKS5, P20, DC12, and DH6. Designed to an ultra-high precision of 0.001mm and achieving a hardness of HRC 58-60, these parts are processed using advanced techniques such as CNC machining, wire cutting, EDM, and deep hole drilling. To enhance performance and durability, they undergo specialized surface treatments like nitriding, carburizing, annealing, normalizing, quenching, and tempering, ensuring they meet the stringent requirements of fuel system applications.
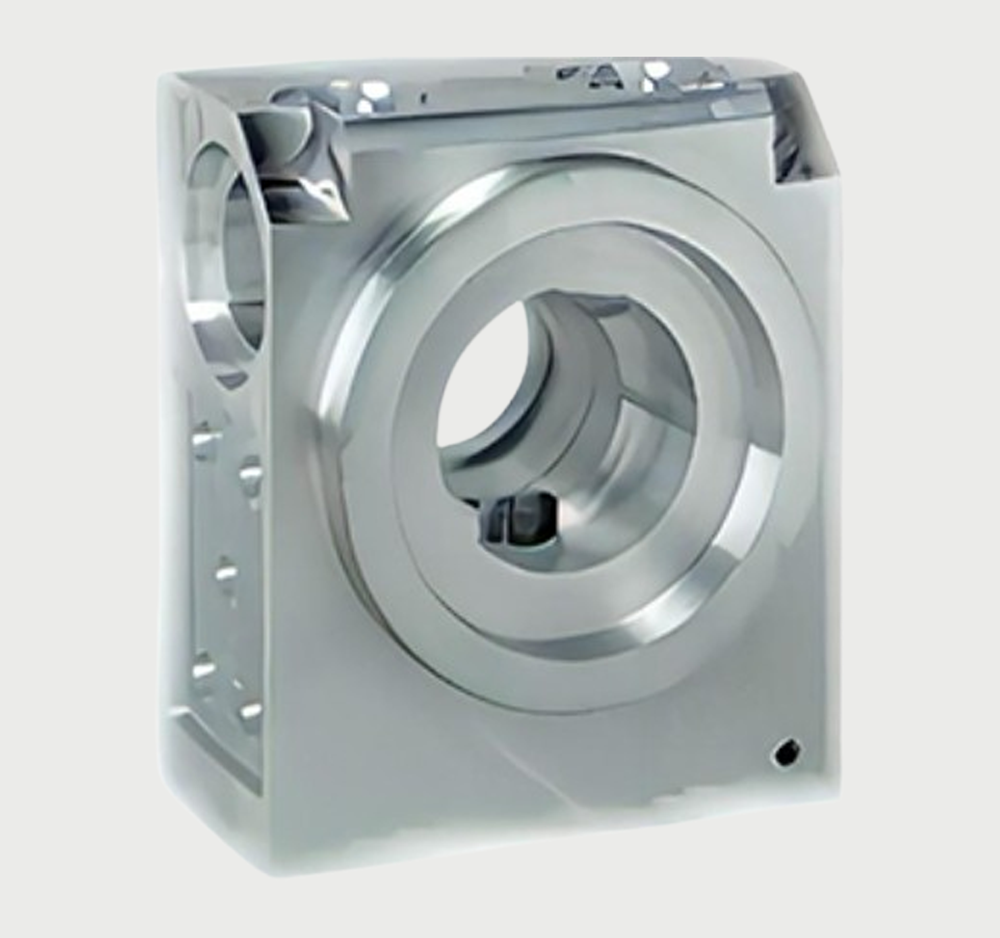
Moduel parts
Module parts are precision-engineered components with dimensions of 3.0x40x65mm, crafted from high-performance materials such as Monel 400, Monel 500, 2.4360, UNS N04400, Hastelloy, soft magnetic alloys, and Inconel 718. With an exceptional accuracy and flatness of 0.005mm, these parts are manufactured using advanced techniques, including CNC machining, five-axis machining, surface grinding, and internal and external cylindrical grinding. To ensure superior surface quality and corrosion resistance, they undergo specialized surface treatments such as electrolytic polishing and passivation, guaranteeing reliable performance in demanding applications.
Five-axis machining Information
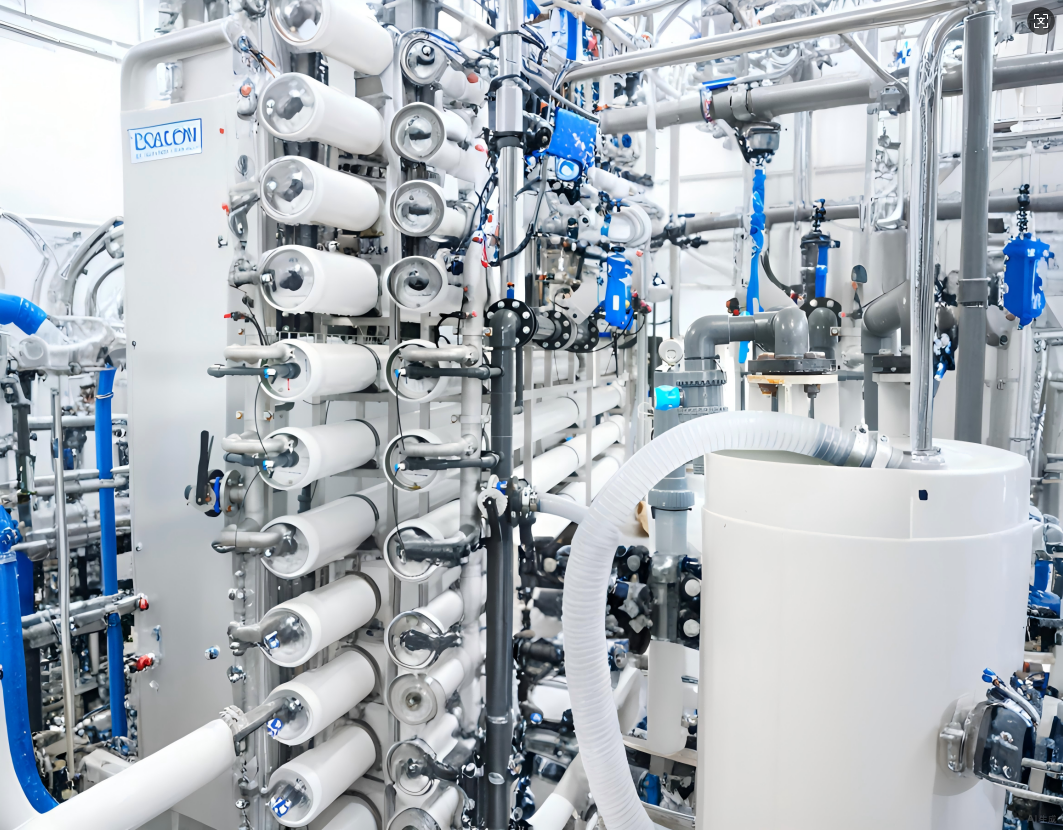
CNC Precision Machining: Mastering Micron-Level Accuracy with ZKPTC
With over 80% of Fortune 500 manufacturers requiring sub-0.01mm precision, modern CNC systems must deliver more than just basic milling. Here’s how ZKPTC’s ISO 13485-certified factories are redefining precision standards
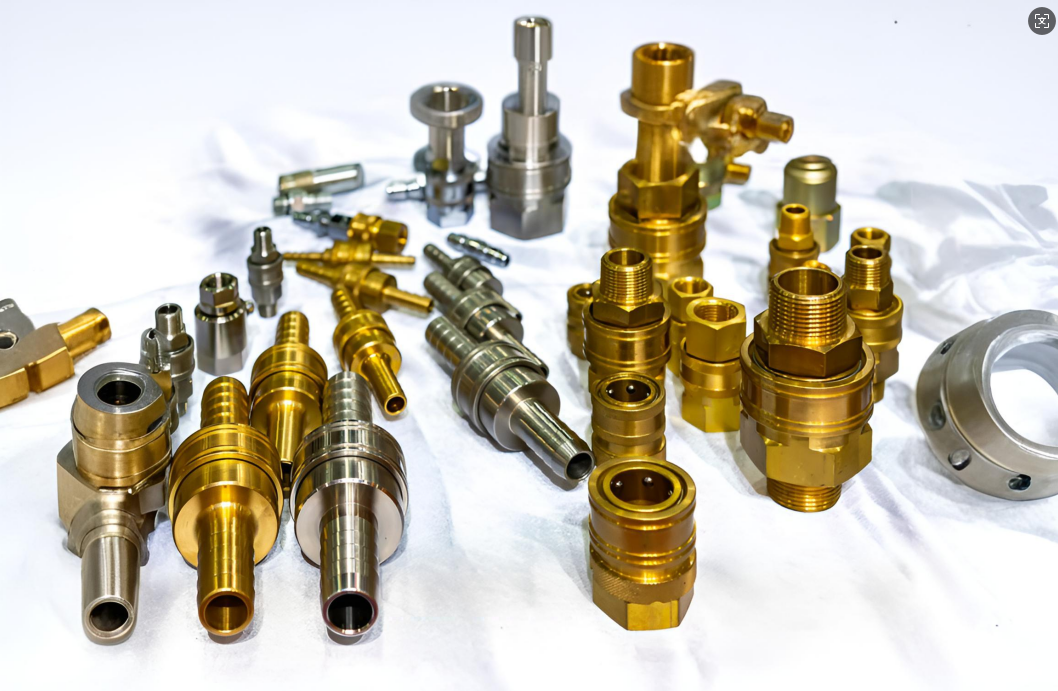
Precision Parts Machining: A Complete Guide to Techniques, Applications, and Industry Solutions
Introduction to Precision Parts Machining Precision parts machining is the backbone of modern manufacturing, enabling industries to create components with unmatched accuracy and consistency. From automotive engines to medical
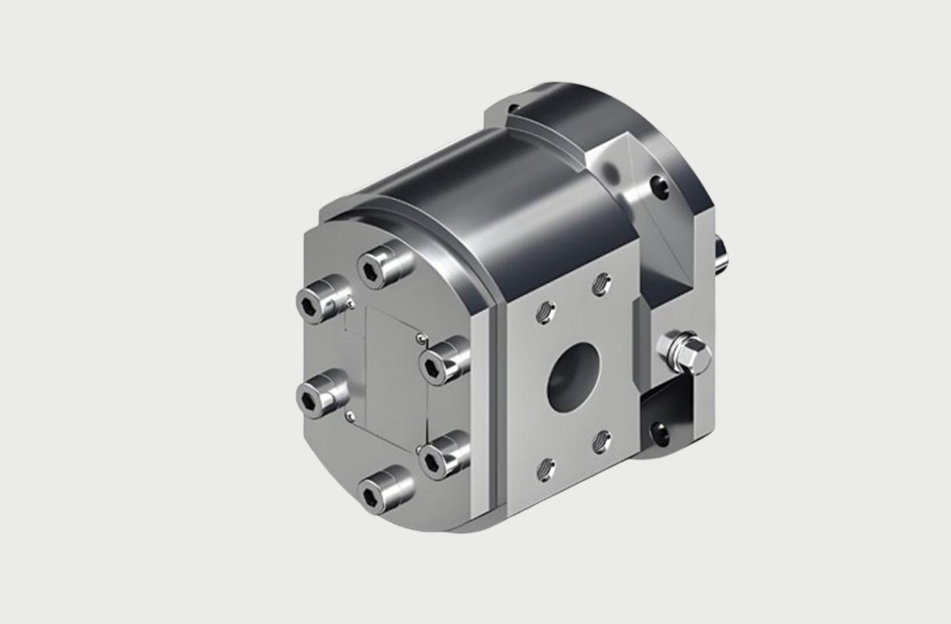
Mastering Five-Axis CNC Machining: Precision Solutions with ZK Precision Technology
Introduction to Five-Axis CNC Machining Five-axis CNC machining is revolutionizing manufacturing by enabling the creation of intricate components with unparalleled precision. This advanced technology, which allows simultaneous movement along five
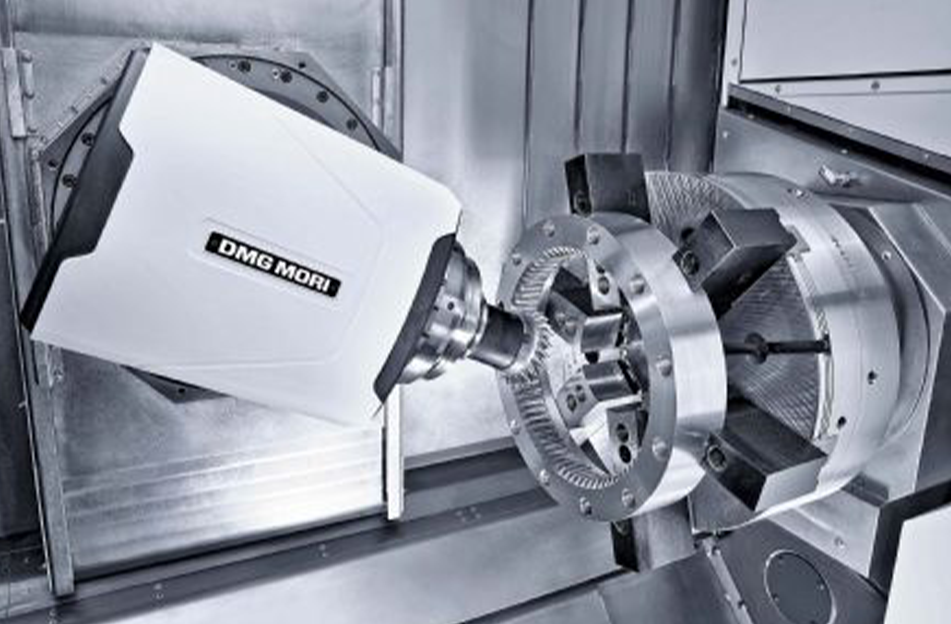
5-Axis Equipment Processing: Elevating Manufacturing Precision with ZKPTC
Introduction to 5-Axis Equipment Processing In modern manufacturing, precision and efficiency are no longer optional—they are essential. 5-axis equipment processing stands at the forefront of machining technology, offering unparalleled capabilities