Introduction to CNC Manufacturing in Industrial Equipment
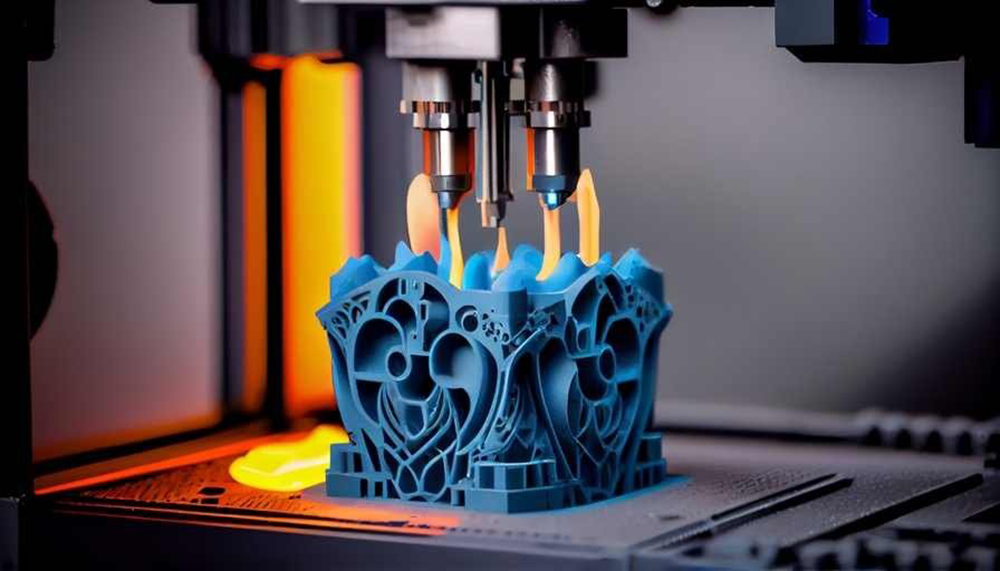
Key Components Produced Through CNC Manufacturing for Industrial Equipment
Structural Frames and Support Components
Structural integrity is essential in industrial machinery. CNC machining allows us to produce robust frames and support structures that ensure stability and durability even under heavy loads. At ZKPTC, every frame is precision-engineered to meet exact specifications.
Gears, Shafts, and Drive Mechanisms
Smooth operations in industrial equipment depend on gears and shafts that fit perfectly. CNC technology produces these components with exceptional accuracy, minimizing friction and maximizing efficiency.
Hydraulic and Pneumatic System Parts
Hydraulic and pneumatic systems require precision valves, connectors, and pressure components. With CNC machining, these parts are manufactured to deliver seamless functionality in demanding industrial environments.
Electronic Housing and Enclosures
Protective housings for electronic systems must withstand harsh industrial conditions. CNC machining produces durable, custom-fit enclosures that shield sensitive equipment effectively.
Advantages of CNC Manufacturing for Industrial Equipment
High Precision and Accuracy
CNC technology ensures every component meets exact design specifications. This level of precision reduces errors, minimizes downtime, and enhances overall equipment efficiency.
Scalability and Mass Production
Whether it’s small-batch prototyping or large-scale production, CNC machining delivers consistency and reliability across every unit.
Material Efficiency and Waste Reduction
Advanced CNC systems optimize material usage, minimizing waste and reducing production costs without compromising quality.
Reduced Downtime and Maintenance Costs
CNC-manufactured parts are built to last, minimizing breakdowns and lowering long-term maintenance expenses.
Materials Commonly Used in CNC Machined Industrial Equipment Parts
Steel Alloys
Steel is renowned for its strength and durability, making it ideal for heavy-load industrial components like gears and structural supports.
Aluminum Alloys
Lightweight yet strong, aluminum is frequently used in industrial frames and high-performance equipment.
Brass and Copper
These materials are essential for precision electrical connectors and heat-dissipating components.
Engineering Plastics
High-performance plastics, such as Nylon and POM, are used for non-load-bearing components requiring chemical resistance and reduced weight.
Applications of CNC Machining Across Industrial Sectors
Construction Equipment
CNC-machined parts are crucial for cranes, excavators, and concrete mixers, ensuring operational safety and efficiency.
Energy Sector Equipment
Wind turbines, oil rigs, and energy storage systems depend on precision-engineered CNC parts for uninterrupted performance.
Automation and Manufacturing Systems
Robotics and automated assembly lines use CNC components for seamless integration and precision movement.
Heavy Machinery
CNC technology supports the creation of engine components, hydraulic systems, and wear-resistant parts for heavy-duty applications.
Quality Assurance in CNC Manufacturing for Industrial Equipment
Adherence to Industry Standards
At ZKPTC, we strictly comply with ISO 9001 and other global certifications, ensuring every product meets industry benchmarks.
Advanced Inspection Technologies
Technologies such as Coordinate Measuring Machines (CMM) and stress testing validate precision and structural integrity.
Traceability and Documentation
Comprehensive documentation ensures every component can be traced back through the manufacturing process for complete accountability.
Choosing the Right CNC Manufacturing Partner
Experience and Expertise
Partnering with an experienced CNC manufacturer like ZKPTC guarantees high-quality, reliable components.
State-of-the-Art CNC Technology
Equipped with cutting-edge multi-axis CNC machines, we meet the most demanding industrial requirements.
Customization and Flexibility
Every project is unique, and we offer tailored solutions to match your specific needs, from prototypes to full production runs.
Future Trends in CNC Manufacturing for Industrial Equipment
Smart Factories and Automation
Integration of AI and IoT technologies in CNC systems enhances efficiency and predictive maintenance.
Sustainable Manufacturing Practices
Eco-friendly materials and energy-efficient processes are shaping the future of CNC manufacturing.
Hybrid Manufacturing
Combining CNC machining with 3D printing enables innovative design possibilities and streamlined production.