Aerospace Industry
Aerospace Precision Machining with ZK Precision Technology
With over a decade of expertise, ZK Precision Technology is a trusted partner in the aerospace industry, delivering high-quality prototypes and production parts with precision and reliability. Our advanced CNC machining and 5-axis capabilities ensure complex components meet rigorous industry standards, while our scalable production systems accommodate small batches to large-scale orders. ISO-certified and backed by skilled engineers, we combine cutting-edge technology with efficient processes to provide affordable, fast, and innovative solutions for critical aerospace applications
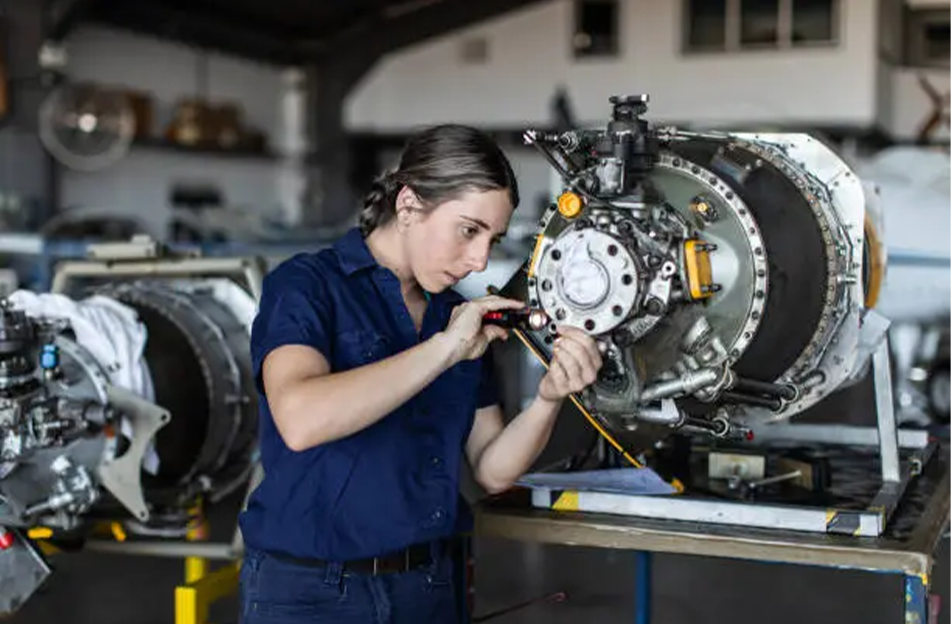
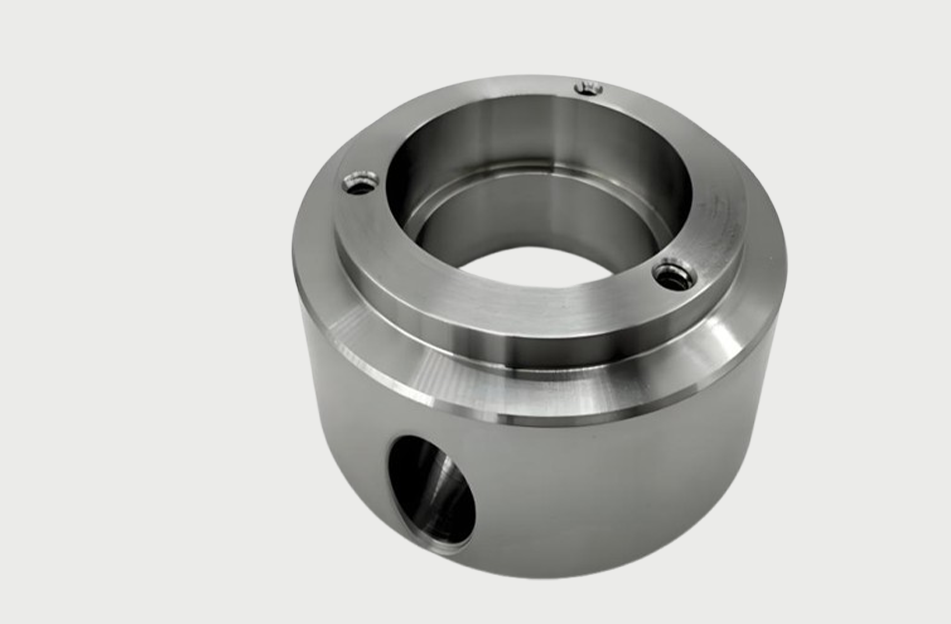
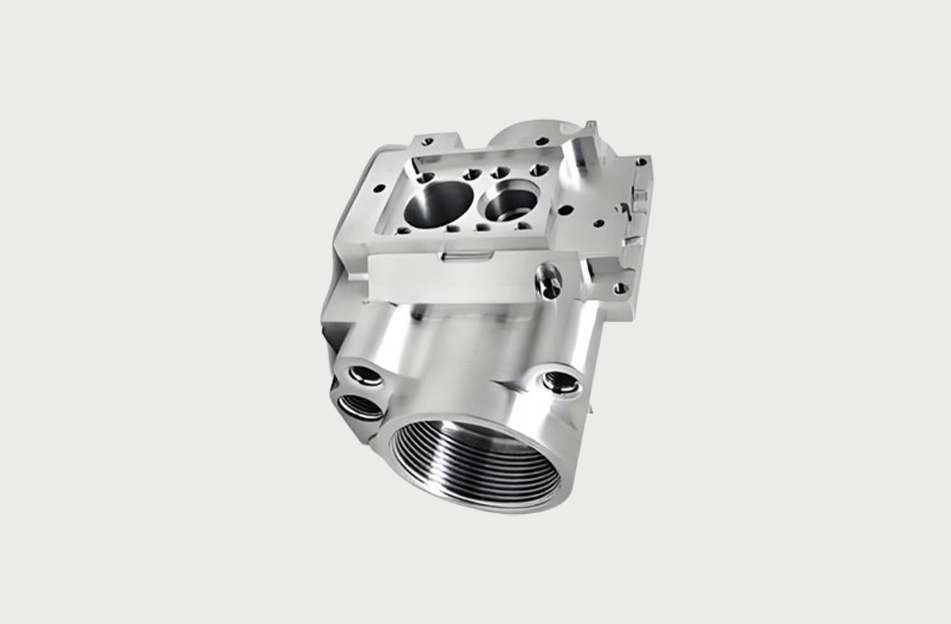
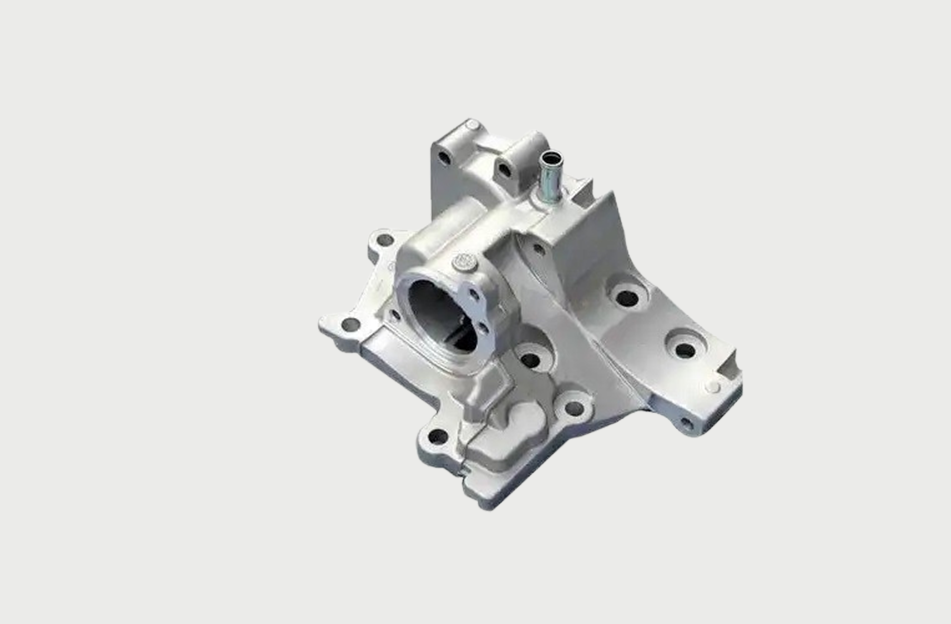
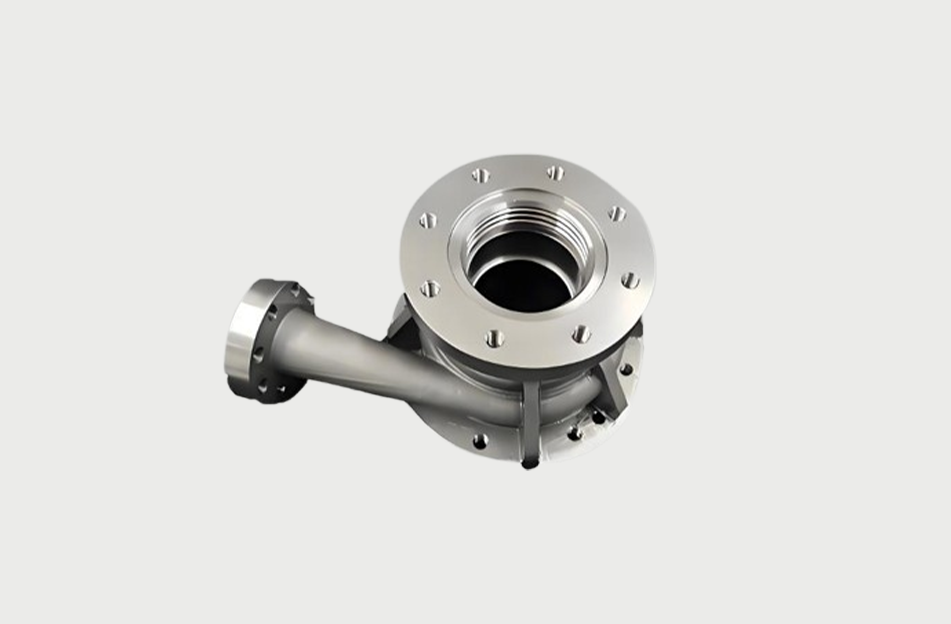
FAQs
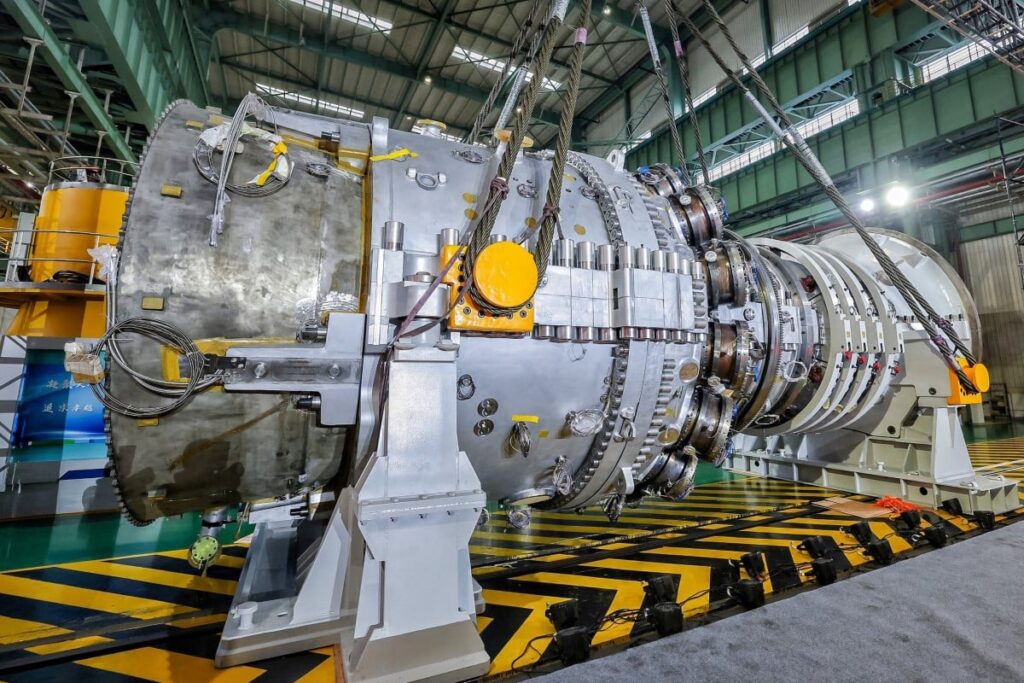
Our company adhere to AS 9100 ensuring quality standard and safety
Our technical team has honed its expertise through diverse aerospace projects, equipping us to deliver fully comprehensive manufacturing solutions tailored to tackle even the most complex machining challenges.
ZKPTC is capable of processing a wide range of advanced materials for the aerospace industry, including titanium alloys, aluminum alloys, high-strength steels, composites, and heat-resistant superalloys
You can ensure you’re receiving quality parts through rigorous quality control processes, including advanced inspection techniques like CMM (Coordinate Measuring Machine) measurements, precision testing, and adherence to industry standards such as AS9100 for aerospace. Additionally, certifications, material traceability, and consistent performance reviews further guarantee the reliability and precision of the parts.
ZKPTC provides dedicated communication support through a single point of contact, regular progress updates, and responsive customer service. They ensure transparency and timely collaboration via email, phone, and virtual meetings to address your needs and keep you informed throughout the project.