High and Low Pressure Fluid
High and Low Pressure Fluid
At ZK Precision Technology, we specialize in delivering precision-engineered components for the high and low-pressure fluid industry, including fluid connectors, fluid sensors, and fluid control systems. With ISO 9001:2015 certification, we ensure every part meets the demanding requirements of fluid engineering applications. Our advanced CNC machining capabilities produce high-performance parts with tight tolerances, ensuring seamless integration and reliability under varying pressure conditions. Whether for prototypes or large-scale production, our skilled team, extensive facilities, and fast lead times guarantee exceptional results, supporting innovations in fluid dynamics and engineering.


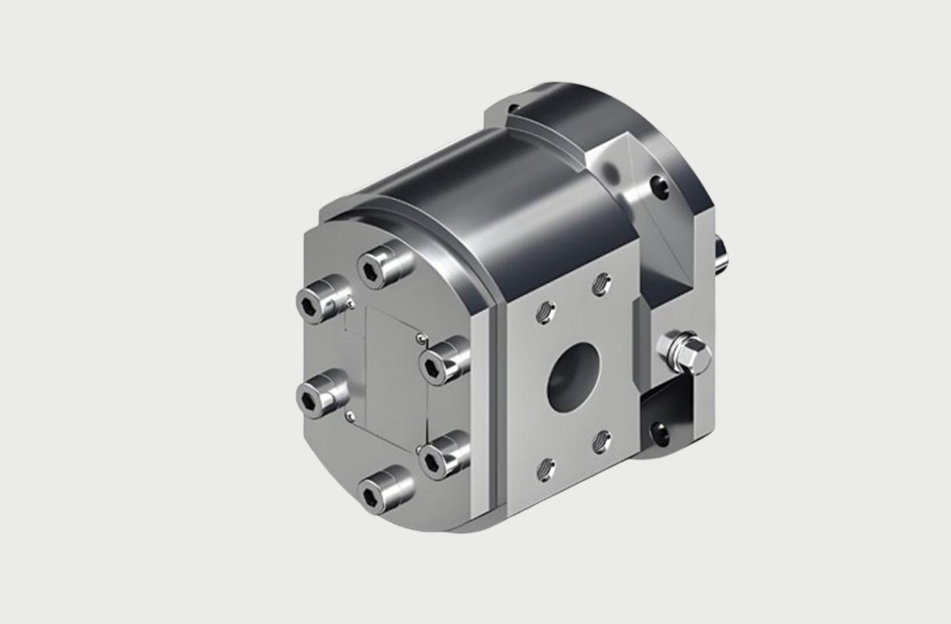


FAQs

Materials like stainless steel, brass, aluminum, and high-performance plastics (e.g., PEEK, PTFE) are frequently used for their corrosion resistance and pressure-handling capabilities.
Examples include fluid connectors, flow regulators, valves, nozzles, housings, and fluid sensors.
Smooth finishes are often required to minimize flow restrictions, prevent corrosion, and ensure tight seals. Polishing, anodizing, and passivation are common surface treatments.
Lead times depend on complexity and volume but are typically 1–3 weeks for most fluid components, with prototypes often delivered in matter of days.
ZKPTC adheres strictly to SOP and PDCA principles, exceeding conventional inspection standards by employing a comprehensive range of go/no-go gauges and threading gauges. These advanced tools ensure the precise measurement of critical dimensions for high-pressure fluid components, guaranteeing consistent quality and reliability.